Last update: Nov 19, 2024
The Rise of the Digital Twin: How Virtual Models Are Reshaping Manufacturing
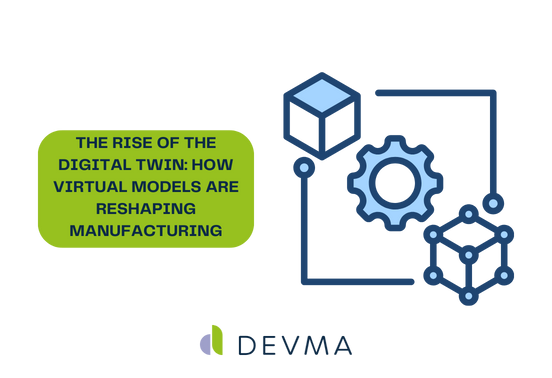
Table of contents
For manufacturers, any edge is a win—no matter how “boring” or cutting-edge it may be. And one of those cutting-edge innovations right now is the digital twin—a virtual replica of physical assets, systems, or processes. This technology is transforming how manufacturers operate by allowing for real-time monitoring, predictive maintenance, and better decision making. At Devma, we see digital twins as game-changers in optimizing efficiency, reducing costs, and making higher quality products.
What is a Digital Twin?
Let’s clear this up: When we say digital twin, we’re not talking about your little bitmoji or new avatar on your Meta Quests goggles. A digital twin is more than a 3D model of a product or system. They tend to be living, breathing, dynamic digital representations that mimic the behavior, performance, and properties of their real-world counterparts. Powered by data from sensors, IoT devices, and machine learning algorithms, the digital twin evolves in real-time, allowing manufacturers to visualize how a product or process will perform under different conditions without the need for costly physical testing.
Moving From Reactive to Proactive
Back in the day, manufacturers fixed machines when they broke and dealt with quality issues after the fact. With digital twins available for use, companies can shift to a proactive stance. Real-time data and visualization allows for predictive maintenance, where issues can be identified and addressed before they disrupt your production. This reduces downtime and extends the lifespan of machinery, ultimately saving time and money. In short, you’re staying ahead of your problems.
Smarter Production
With a digital twin, you can simulate production processes before it even begins. Want to know how a new assembly line will perform? Or whether introducing new material will impact efficiency? Well, a digital twin allows you to test these scenarios in a virtual environment so your “trial and error” isn’t so detrimental. By adjusting variables like machine speed, material flow, or worker interactions, manufacturers can find the most efficient methods of production.
Product Quality and Innovation Matters
Making sure your quality is up to par is one of the most important things you can do in manufacturing. Digital twins are revolutionizing this space as well. With a virtual model mirroring the real-world in every detail, manufacturers can identify flaws or performance gaps early in the design phase. This speeds up the product development cycle and ensures that by the time a product reaches the shelves, it has been fine-tuned to perfection.
Digital twins also open the door to innovation. By experimenting with different designs, materials, and processes in a digital environment, manufacturers can push the boundaries of what’s possible – introducing new products faster and with less risk.
Digital Twins are the Future of Manufacturing
At Devma, we know and believe that digital twin technology is a vital component of Industry 4.0, the fourth industrial revolution. As more manufacturers integrate these models, we’ll see smarter factories, increased automation, and heightened ability to adapt to market demands in real time.
With the power to predict, simulate, and optimize every step of the manufacturing process, digital twins are reshaping the future of the industry. And the future looks brighter and more profitable than ever before.